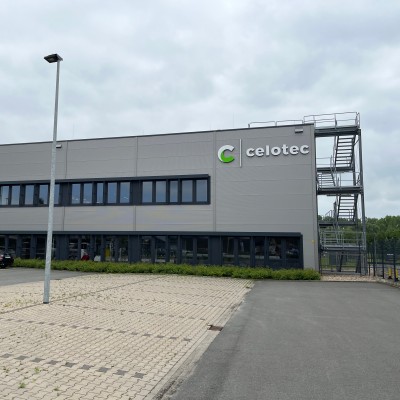
Masterdata team visits surface specialist celotec
The WinDo Experts masterdata team visiting the surface specialist celotec
At the end of May, our colleagues of the WinDo Experts masterdata team visited the sister company celotec in Sendenhorst. The reason for the visit was the introduction of the new fine structure surfaces at the system provider VEKA as well as the production process for this new type of foil.
They were welcomed to celotec's state-of-the-art factory by technical manager Michael Janning. After an initial overview of the company's history and the entire product range, they went on to the exhibition, where they first examined the samples of the fine-textured surfaces. This is a high-tech development with a particularly hard-wearing lacquer surface on a PVC base film. The new fine structure is inspired by the popular aluminum powder coating of the same name and is even more resistant to external influences.
Revolutionary surfaces for interior and exterior
After the exhibition, we went to the large production hall with the impressive roll-to-roll coating line. Here, films are coated with a special ESH coating at speeds of up to 150 meters per minute. The heart of the unique coating system is a so-called e-beam, in which the coating on the films is irradiated with electrons. This causes a chemical reaction so that the special varnish hardens and forms a surface that is particularly robust against various chemical, mechanical and environmental influences. The result is a surface that is extremely weather-resistant, durable and abrasion-resistant.
These high-quality surfaces with the brand name spectral are not only used in window construction, but also for other building products such as door panels, garage doors and facade elements. For example, unlike conventional window surfaces, celotec foils can be chemically cleaned and do not change their gloss level even when bending round arches. Coating mixing and development is carried out in the company's own coating laboratory and is one of the major innovations in the foil industry.
Furthermore, the celotec product range also includes films for building interiors. These films, available under the brand name celobon, are manufactured using the same technology and are used laminated on panels as flooring, wall and ceiling cladding or even interior doors and window sills.
"Experiencing live that celotec surfaces are not embossed was an absolute highlight. The structuring, such as ultramatt or fine structure, is introduced directly into the coating layer using different processes when the coating is cured," summarizes Dominik Blumberg, Product Specialist Master Data Service WinDo Experts.
At the end of the tour, a visit to the converting department and the warehouse was on the agenda. The line can produce rolls of foil up to 1.60 m wide. The coated films are then cut to the width required by the customer. Any defects are automatically registered by the coating system during production and removed during packaging for the finished product, so that only flawless products are delivered to the customer.
Quality tested in the celolab
Quality is a top priority at celotec. With this in mind, the masterdata team was also allowed to take a look at the company's own laboratory, celolab. There, different weathering and aging tests are carried out on the surfaces. During the simulation of environmental influences, the surfaces are tested for durability and color fastness. Alternating exposure to UV and xenon radiation as well as sprinkling and high-temperature tests artificially accelerate weathering. Celotec carries out these tests not only for window profiles, but also for the automotive industry, for example.
The application technology development and testing of the foils is another important aspect. For example, a laminating line is available in celotec's foiling technology center for laminating foils with appropriate primer adhesive systems onto profiles and sheets made of a wide variety of materials.
Latest masterdata via WinDo Experts
The background to the company visit at celotec is the upcoming master data updates. Through our update service, we provide our customers with all current surface designs of the system providers VEKA and GEALAN in a timely manner and in a manner that is reliable for orders. With the material price updates, our contractual partners also receive the current prices for calculation on a monthly basis. In this way, our customers benefit from up-to-date master data that they don't have to worry about themselves. This leaves more time for the core business.
We would like to thank the entire celotec team and especially Mr. Michael Janning for the successful factory tour. The tour was highly interesting and Mr. Janning took a lot of time. He explained the complete process with a lot of passion and competence and answered all our questions. The masterdata team is now going back to their tasks with different eyes. We are especially excited about the new and promising fine structure surface to see how this will be accepted in the market. In any case, it is already included in the new WinDo Experts masterdata.
You can find out more about celotec's innovative surfaces on the website:
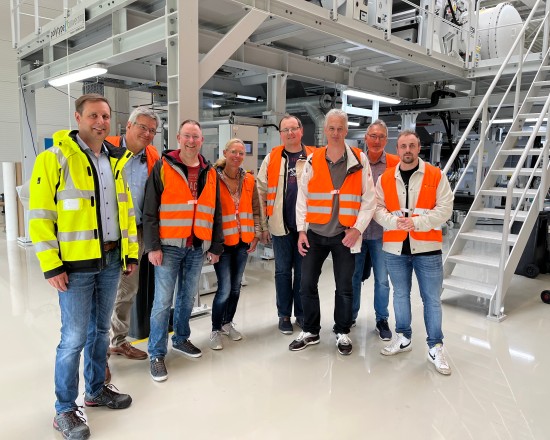
The WinDo Experts masterdata team visiting the surface specialist celotec.
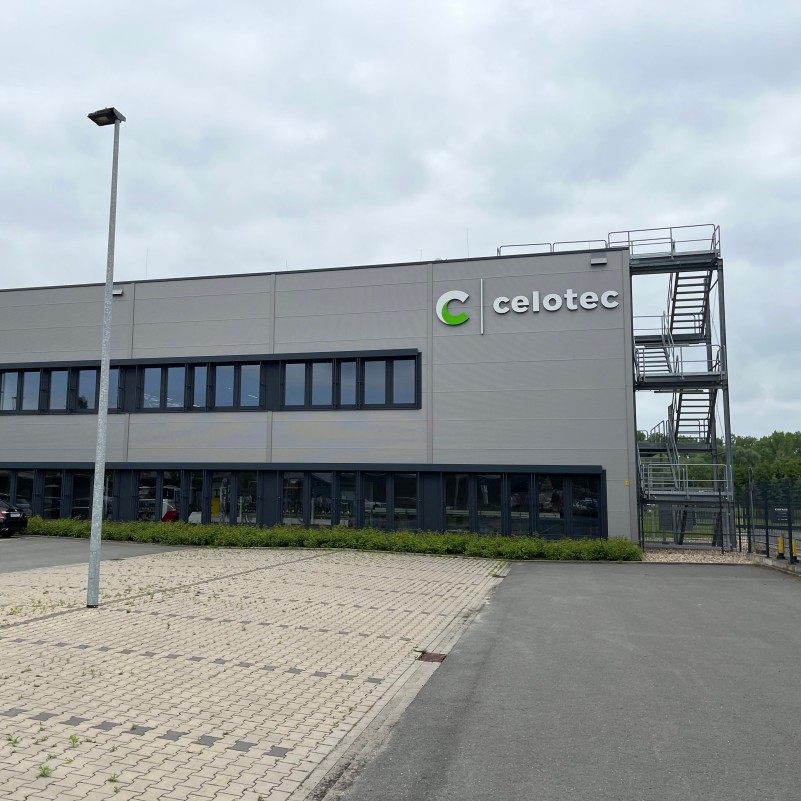
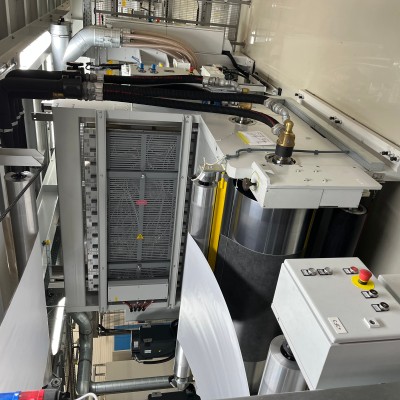
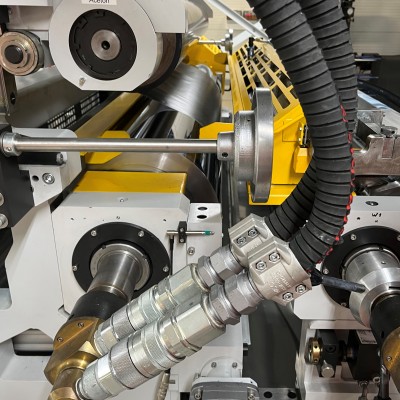
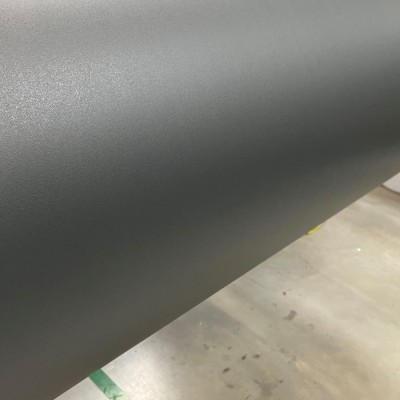
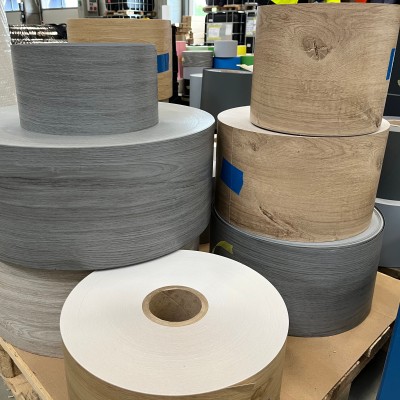
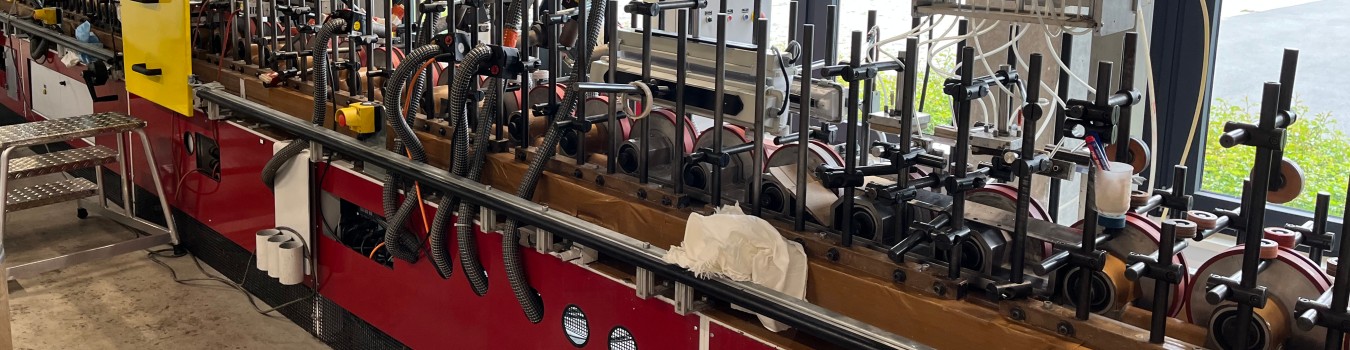
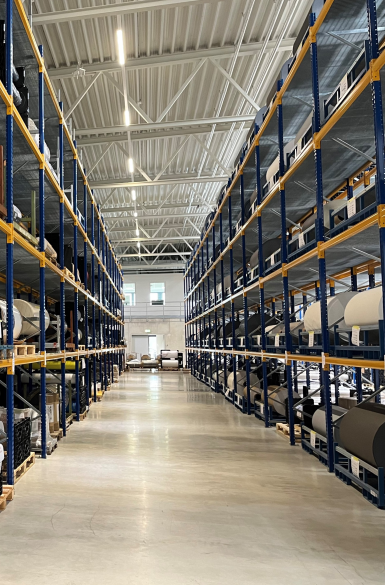
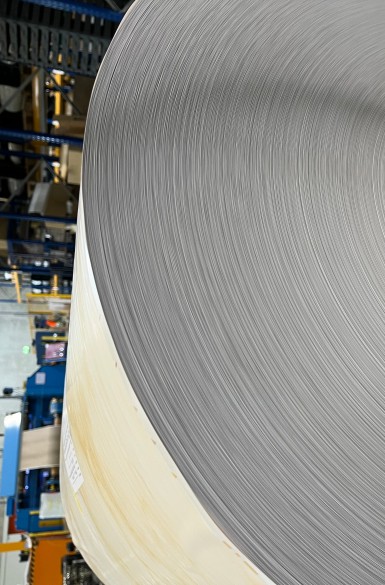
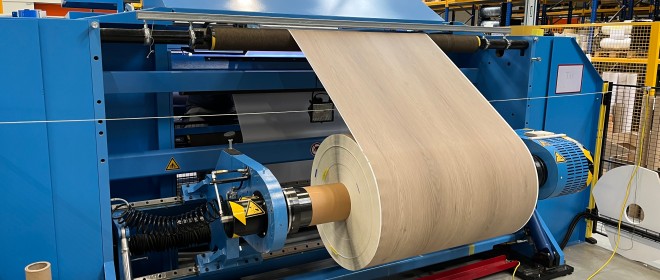
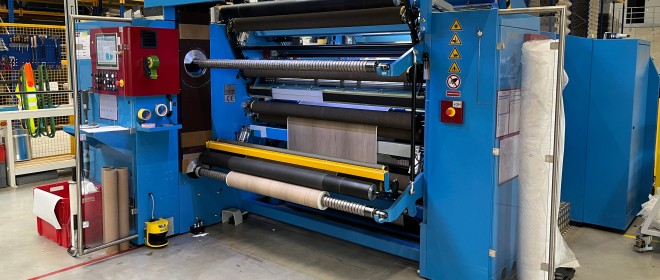